TM 10-4330-237-13&P
1.9 LOCATION AND DESCRIPTION OF MAJOR COMPONENTS. (Refer to figure 1-2.)
The liquid fuel filter-separator is an aluminum vessel (1) with an integral frame and is designed to house three coalescer
elements (2) and a separator element (3). A sump (4) at the bottom of the vessel (1) collects water and sediment
removed from the pumpage by the filter action. A diverter plate (5) located directly behind the inlet port (6) prevents the
incoming pressurized pumpage from directly impacting the filter elements (2 and 3) and equalizes pressure across the
inlet bulkhead (7). The coalescer elements (2) are one-piece, closed end, threaded-base elements and are retained to
the inlet bulkhead (7) by threaded-base adapters (8). The separator element (3) is a one-piece, monel or stainless steel
screen coated on both sides with Teflon. It seats over a threaded rod (9) into a friction fit adapter (10) on the inlet
bulkhead (7). All four elements are retained in position at the cover (11) end by a cross shaped element retainer (12). An
O-ring (13) and a domed aluminum cover (11) seal the access end of the vessel (1). Two handles (14) are provided on
the cover (11) for removal and replacement of the cover (11).
3-inch valved unisex couplings (15) bolt to the flanged outlet (16) and inlet (6) ports for interface to the system fuel
discharge hoses. Dust caps (17) are provided to protect the unisex couplings (15) when fuel hoses are not connected. A
2-inch valved unisex coupling (18) with a pipe thread adapter is fitted to the sump (4) to provide a drain/defuel connection
to the system or an auxiliary pump. A pipe plug (19) located on the bottom of the vessel (1) near the inlet port (6) drains
the cavity formed by the inlet bulkhead (7) and the diverter (5). Air is vented from the module through a manual 1/4 turn,
spring loaded vent valve (20) located on top of the filter vessel (1). A standard fuel sampling port (21) is fitted into the
outlet port (16) for fuel testing.
Filter status is monitored by a sight gauge (22) and a differential pressure gauge (23). The differential pressure gauge
(23) is connected by hard tubing between the inlet (6) and outlet (16) ports to measure the pressure drop across the filter
vessel (1). A clean, properly operating system will register 2-3 pounds differential pressure. The pressure drop will rise
gradually as the elements become contaminated by use. When the pressure reaches fifteen pounds, the coalescer
elements (2) should be changed and the separator (3) thoroughly cleaned. A sudden drop in pressure indicates that fuel
is flowing through the filter vessel (1) without resistance, probably indicating a ruptured element (2 or 3). A sudden
increase in pressure indicates a blockage due to a malfunction or ingestion of a foreign object. The sight gauge (22) on
the vessel sump (4) provides visual indication of the amount of water collected in the sump (4). A ball in the sight gauge
(22) will float on water but not on fuel, providing a direct indication of the amount of water in the sump (4).
1.10
EQUIPMENT DATA.
The following is a tabular presentation of physical and performance data required for operation and/or unit level
maintenance.
Table 1-1. Equipment Data
Description
Quantity
Leading Particulars
Liquid fuel filter-
1
Shipping Volume:
15.3 cu ft (0.43m3)
separator
Weight (Dry):
137 lbs (62.1 kg)
Weight (Drained):
147 lbs (66.7 kg)
Weight (Full):
317 lbs. (143.8 kg)
Length:
55 in (1397 mm)
Width:
20 in (508 mm)
Height:
24 in (609.6 mm)
1-5
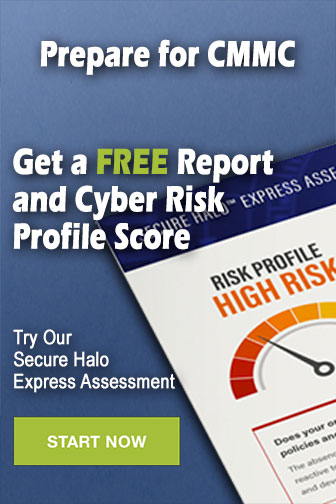